INTRODUCTION
It is not widely apparent to the fire protection engineering community that the emergency communications systems (ECS) cable product known to address UL 2196 for fire resistive electrical cable assemblies known as circuit integrity, mandated by NEC and NFPA, is only produced by two firms. We question if production and types are adequate to meet varying needs and/or applications, as well as at a cost that provides a product within established infrastructure capacity for installation into buildings and structures.
The following is our review of fire resistive cables for electrical circuit integrity, or CI as it is known, under the NFPA 72-2010 standards for ECS, pathway survivability level 2 or 3 as mandated by Paragraph 24.3.5.41 in the standard to withstand a UL rating of two-hours under 1850°F fire conditions. This actually includes over three hours of intense direct flame and heat applied to cables and assemblies during the test, with a light bulb working to prove “success.”
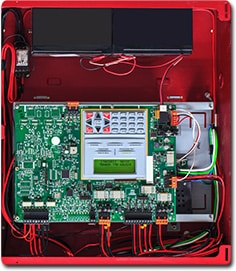
This standard applies only to ECS systems – NOT, sensing, initiating, or control cabling, unless part of the continued operation of the ECS electronics.
Approved cable product listings are currently only being provided by two manufacturers in the United States, with limited wire jacket, construction types, and availability to meet fire alarm equipment specifications; making it potentially unuseful for a fully compliant installation. This may be required by local code to provide complete integrity within riser raceway enclosures since only specially listed power limited CIC approved cables, or CI cables listed for use in EMT conduits, must be used.
In contrast to the need to use CI listed cable, the use of previously approved cables provided for a temperature of either 150°C Halar/Kynar jacket wrapping, or a 200°C Teflon composition.
FIRE ALARM CABLE HISTORY
Before 1970, many fire alarms were wired with chemically impregnated cloth-covered solid copper wire which deteriorates as a cable assembly with the cover often oxidizing, drying, and fraying. Many systems exist with this previous combination of aged cable. Some in fact still carry 220v DC for smoke detection and fan control in basements of older properties, especially in New York City.
Between 1976 and 1990, fire alarm cables became fairly utilitarian and quite similar to the cables used for electrical wiring, audio, and electrical application. In many cases, even electrical wire such as THHN were used. By the mid-1980s, jacket colors were added and new compounds for fire alarm cables were constructed. By 1995, Teflon and Hypalon were both being used as cabling to connect fire alarm equipment. Even audio cables which require special construction and low capacitance were provided with improved fire resistant constructions.
By year 2000, tests were conducted and compounds were improved even further. But Hypalon was found to fail the UL 1685 “limited smoke test.” New compounds are now available, including Teflon which meet both smoke and flame tests, but are not rated for ‘CI’ or ‘CIC’ assembly use, although still meeting 200°C testing.
In 2001, one of the most destructive events in American history occurred with the collapse of both World Trade Centers. The air-laden bomb explosions caused such devastation to the internal structure that the heat, flames, and resultant penetration of liquid fuels into the building core and structural steel’s implosive removal of fire proofing compromised the integrity of the fire alarm communications system. NFPA through the AHJ’s and manufacturers representing these code committees required greater cable performance from cables both in conduit and behind walls to assure performance under the most intense conditions.
Cable not in conduit constitutes a large part of a building’s signaling cable. The idea to resist fire within the two-hour UL requirements is, in fact, difficult to meet and is not without technological hurdles and repercussions. Unintended consequences may be the resultant description of this “improvement” to technology to saving lives and property.
COMPOUND PROBLEMS WITH PROBLEM COMPOUNDS
By 2010, many of the CI cables that were produced around the country were being installed in buildings within an acceptable margin of construction cost. While these cables would easily compare to the cost of higher degree-rated cables, the costs should have been low enough to save on installation costs by reducing the need for expensive horizontal runs of conduit. In fact, this was the case until 2012.
At least 75% of many building horizontal feeds of cable could be installed without conduit. But with standards come listings. Fire requirements reflected a new UL requirement requiring retesting of all cables by all manufacturers.
One manufacturer from the greater northeast of the United States submitted two spools. The first test burned and passed. The next test burned and failed, while the next test burned and passed, and so on. Discrepancies such as this should not occur, especially not repeatedly for all manufacturers who themselves tested their products prior to shipping in strict conformance to guidelines expected for full test compliance under UL procedures.
Interestingly, it was noted in posted articles and in a PowerPoint presented to San Francisco’s IEEE section organization by one manufacturer that the very conduit which it was supplied by UL to test effects of heat, effectively contributed to the failure due to zinc coatings bonding to the cable and destroying it within the conduit. Only organic coatings must be permitted to now meet the CI assembly requirements.
UL summarily withdrew all product listings that had such discrepancies and notified the manufacturers to pay for the retesting; all while the manufacturers deemed the tests inappropriate and inconclusive. At least one manufacturer insists all tests should be redone free of charge. This impasse has been going on since August 2012 with significant monies and time having both been spent.
It was not until 2014 and 2015 that one of the current “listed” manufacturers received UL approval – a two- and three-year gap without product and over four years after NFPA 2010 was approved.
ALL METALS ARE NOT EQUAL
While we often think of cables as generally conducting electricity, they conduct types of signals including analog, digital, simultaneously both analog and digital, DC for power, and timing signals for synchronized strobes among others. Special compounds are used to reduce capacitance and to construct the jacket with the electrical circuit integrity requirements. Manufacturers may add to the compounds of the jacket particular chemicals that one may not have even expected. Changing physical chemistry properties requires testing. Compounds within the CI or CIC jacketed cable assembly designation provide what is called ceramification upon burning. The thermoplastic portion of the ceramic polymer disintegrates, leaving a fully ceramic layer.
The cable jacket ceramifies into a heat protective sheath allowing conduction of electricity for up to two hours at 1850°F. It is supposed to meet the certification for FPLR, or Fire Protected Power Limited Riser cable as well, while actually being subjected to over three hours of flame and heat. Note that only ECS equipment is required by NFPA 72-2010 to be rated as circuit integrity cable assemblies for emergency communications use.
Many previously approved listings consisted of Halar/Kynar, which were proved technically adequate under Local Law 5. These have higher temperature compounds and are listed as suitable for initiating and signaling circuits, but not under the new ‘CI’ or ‘CIC’ requirements for emergency communications systems.
Moving to Teflon coatings, if you’ve ever manipulated this extremely beefy, well-protected cable capable of operating up to 200°C, then you’ll perhaps understand the dilemma faced by fire protection engineers, electrical contractors, and Owners for ECS systems improvements.
TAKING ADVANTAGE OF A CLOSED MARKET
Fire alarm approved cable using Halar and Kynar for protective ratings of up to 150°C sells for between $.35 and $.45 per linear foot.
Using a Teflon jacket with a 200°C rating, an even higher temperature compound, sells for between $.45 and $.55 per linear foot.
Today, however, there are only two manufacturers making a limited number of fire alarm, CI and CIC assembly approved cables that are UL listed. These two suppliers, which provide cabling in limited construction and availability costs between $3.00 and $4.00 per linear foot, which is approximately eight to ten times the cost of previously available, specialty fire alarm cables.
SAFETY IMPLICATIONS – DRAWING THE LINE
One could argue that the event of 9/11 with two high-rise structures collapsing due to the extreme heat of the fire should require all high rise buildings to employ electrical cable integrity to survive the two hour fire safety rating. And while one may reason that this is an over emphasis of fire safety for tall buildings, you only need count the number of high rises built in the U.S. since 2001 to see how important this fire safety aspect becomes – over 100, including three of the tallest in the world.
But should all high rise buildings have this requirement? Should CI and CIC rated cable assemblies and UL‑listed cable be required for seven stories or forty stories; or 100 stories? Or should there be fire safety risk accommodation to where and how the cable should be applied within each structure?
Should we have the opportunity to utilize building fire protective features of gypsum wallboard or concrete masonry unit (CMU) in front of the cable as an additional rated and approved protective enclosure, similar to plastic fire sprinkler piping which cannot be exposed? Or should we react beyond the expected; that a room completely engulfed in flame, drop ceiling collapsing, cables exposed to over 600°F temperatures, should continue to have available emergency audio communications for two hours continuously within that zone?
I believe meeting three criteria should be considered: 1) is the requirement practical, 2) is there a precedent indicating such measures will actually improve protection of lives in such spaces, and 3) is the improvement technically and financially prudent?
The sheer lack of competitive product and open testing procedures creates holes in compliance. Having limited availability of CI rated cable assemblies which has a singular or limited supply path does not provide the diversity of requirements for complex high rise fire alarm. While simple two-conductor cable is required, most often data grade cable is also required, and special audio cables for particular use to maintain a high fire safety posture within NFPA. It is of no use to have two cables in a fully rated CI system with UL approval when other cables in the raceway cannot meet those same requirements. This creates a hole in our protection.
This is no small matter. The IBC 2018 Edition, the most representative building code in the United States, will require movie theaters, malls, schools, and many more public assembly places to require the meeting of NFPA’s ECS requirements for audio evacuation – mandating once again an expanded use of CI and CIC approved cable assemblies by only limited manufacturing sources at unreasonable costs of materials. But will it work to provide audio under these adverse conditions? Is the improvement technically prudent? Will it actually perform as expected during or after these conditions?
LACKING A TEST FOR AUDIO INTEGRITY
One can predict with great certainty that an audio circuit path using line level (0 dBm) signals, and especially low voltage digital signals (while not even dwelling into the effects onto fiber CI cable), will be: 1) attenuated due to noise, 2) impacted with low- and mid-frequency spikes, and 3) affected adversely to continue operation over this two-hour period.
Forensically, one would expect a percentage of input/output circuitry failure due to overload by excessive microphonics, transient line-induced EMP signals, and impedance shift affecting intelligibility to occur after heat introduction.
Interestingly, the UL procedure provides for a light bulb test – one 120 VAC light bulb needs to work at the end of each test. There is no test to justify and certify continued audio for ECS use with any cable listed by any manufacturer regarding impedance, frequency band width, or noise under these untenable conditions. This in itself compromises that which the listing is to safeguard against – loss of communications.
NEXT STEPS
Permitting by risk analysis higher temperature protective cable coatings behind protected raceways and building structures, similar to the way fire command stations are designed and the way the layout of the entire project from an electronics standpoint is derived, may be a more appropriate solution.
To incorporate fire alarm system risk assessments with limitation to the particular use of specific cables without review, does not meet owners, developers, building engineers, design engineers, building code officials and authorities having jurisdiction expectations when it is not known if the audio portion of the ECS system will even work under fire conditions predicated by the UL test.
Our opinion is that no singular solution with zero alternative options, zero testing of audio capability under intense fire and heat conditions, or one which leverages one or two manufacturers to profit at unreasonable levels, is not a practical solution with sustainable results. The opportunity to employ risk based fire safety measures on cable selection by the Engineer-of-Record for high-rise buildings should be promoted and appended into Codes and Standards immediately.